Machinery / Semiconductors and Automation
Deburring Systems/Wet Blasting Systems, Laser Deburring Systems
Iwatani offers advanced one-stop solutions that encompass all processes encountered in the semiconductor manufacturing sector.
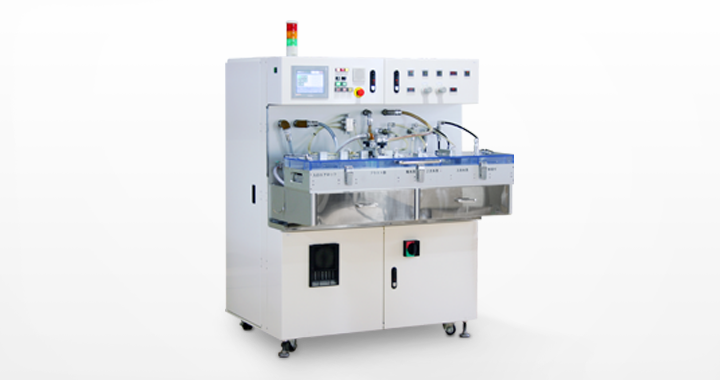
Explanation of Wet Blasting Principle, Wide-Angle Gun (Patented), and Abrasive
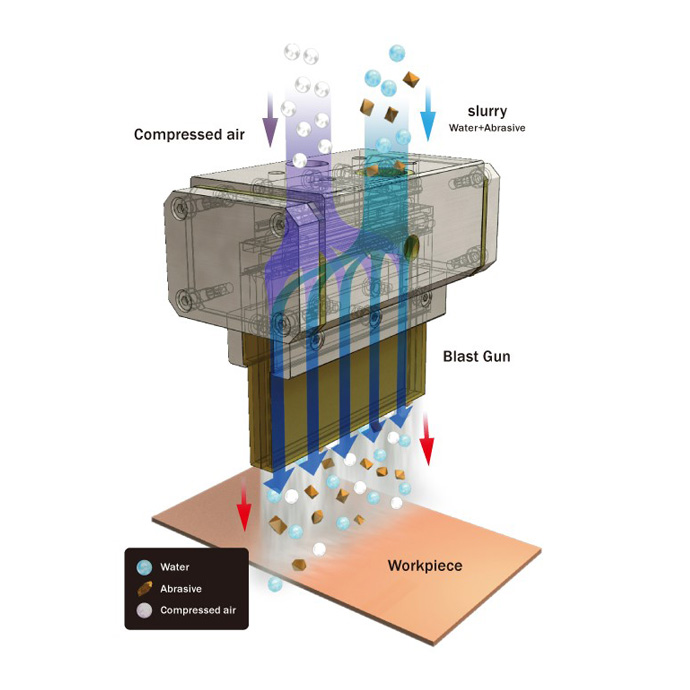
The Principle of Wet Blasting
Wet blasting is a technique used to clean, process, or improve the surface of materials such as metals, plastics, and ceramics by blasting them with a high speed slurry of water and abrasive with a mean particle size of 3 to 300 µm. Wet processing allow use of fine abrasives with a particle size of a few microns, making it also ideal for microscopic processing. Iwatani offers solutions in the form of a wide-angle gun, a proprietary Iwatani technology essential for uniform processing of large areas.
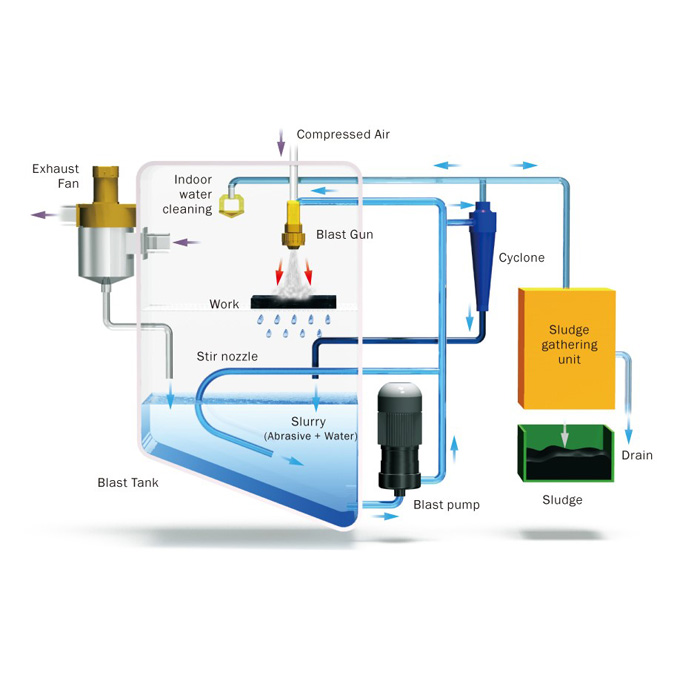
The wet blasting process involves slurry (water and abrasive) that is gathered up from the blast tank by a pump, mixed with compressed air inside the blast gun, then sprayed out. The slurry returns to the blast tank, where it is recirculated and reused.
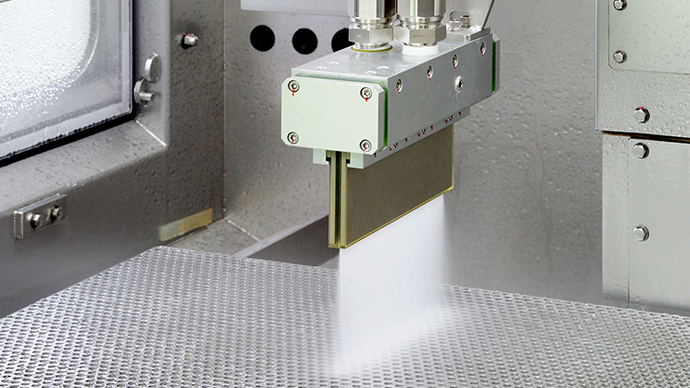
Wide-Angle Gun (Patented)
The wide-angle gun is a spray gun with a slit-style nozzle designed specifically for use with wet blasting. It ensures uniform coverage of the entire area being processed to achieve highly efficient processing, free of unevenness.
Features
- Even processing over entire area
- Can be used even with thin and fragile objects
- Processing with high degree of repeatability and controllability
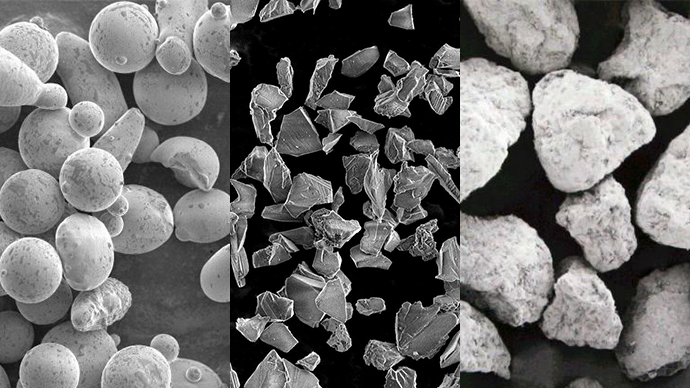
Abrasive
The abrasive used in wet blasting consists of materials such as ceramic, resin, or metal, with the material, shape, and size selected to achieve specific targeted results.
- Ceramic abrasive
Ceramic abrasive is primarily formed of alumina particles of polygonal or spherical shapes. Polygonal particles are used for grinding and roughing, while spherical particles are used for cleaning and cosmetic applications. - Resin abrasive
This softer abrasive allows gentle processing that does not damage the material being processed. It is used for cleaning and resin deburring applications.
Compact Conveyor Type Wet Blasting System
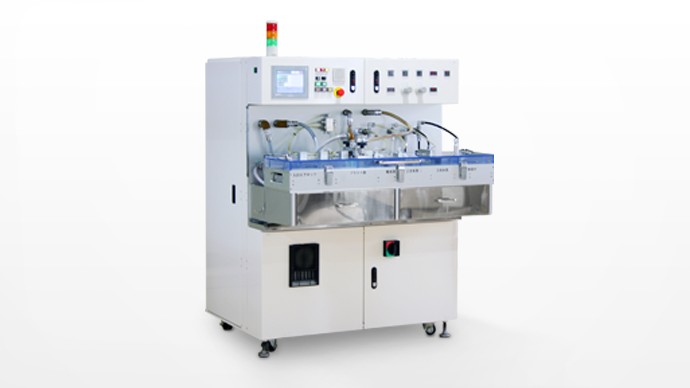
Continuous Automatic System Capable of Processing Both Sides of Strip Material
Incorporating a wide-angle gun designed for use with electronic components such as printed circuit boards and semiconductors, this compact system is capable of uniformly processing both sides of small strips or plate workpieces.
Features
-
Consistent Quality Due to Precision Processing
- The patented wide-angle gun technology developed by the manufacturer ensures uniform processing without unevenness.
- Surfaces can be cleaned or roughened to submicron scales by spraying microscopic abrasive with particle sizes of just a few microns.
-
Improved Work Efficiency
- Since wet blasting is a physical treatment, a wide range of workpiece materials can be processed without resetting the system.
- The compact blast chamber interior allows easy maintenance of the drive unit simply by opening the conveyor cover.
-
Environment
- The wet blasting system prevents dust generation, improving the working environment and eliminating dust explosion hazards.
- Cleaning and processing are chemical-free, eliminating reactive waste and minimizing environmental impact.
Main Applications and Workpieces
-
Flash and Burr Removal
- Removal of thin burrs occurring on lead frames and heat sinks
-
Stubborn Resin Burr Removal
- Removal of stubborn resin burrs such as dam burrs and side burrs adhering to lead frames
-
Surface Cleaning After Ceramic Firing
- Removal of surface powder and nonconductive layers arising during firing
Compact Batch Type Wet Blasting System
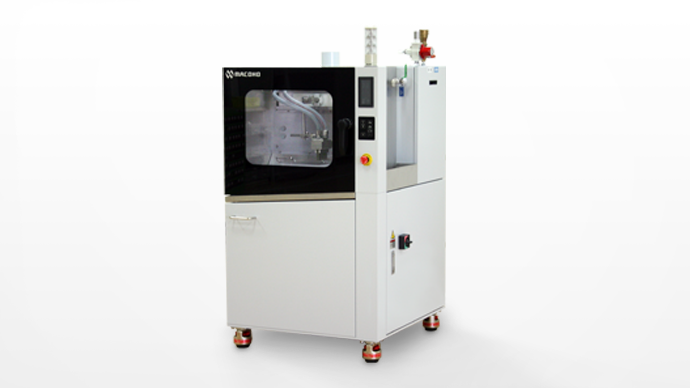
Compact System for Processing Test Pieces Automatically by Moving the Nozzle Along a Single Axis
This compact wet blasting system for R&D applications uses proprietary wide-angle gun technology and single-axis drive to achieve uniform processing. A wide range of surfaces can be formed depending on the abrasive selected, making it ideal for testing and setting parameters.
-
Ideal for R&D
- Compact size ideal for use in research labs
- Extremely low dust emissions during processing eliminates contamination of surroundings.
- Can be used with a wide range of different abrasives, making it ideal for testing and setting parameters.
-
High Processing Repeatability
- Combines a patented wide-angle gun with single-axis drive to achieve remarkably uniform processing.
-
Simple Operation
- Blasting and gun parameters are easy to set.
Main Applications and Workpieces
- Research and development, including test processing and parameter setting
- Processing of small items or small-quantity batches
Manual Wide Wet Blasting System
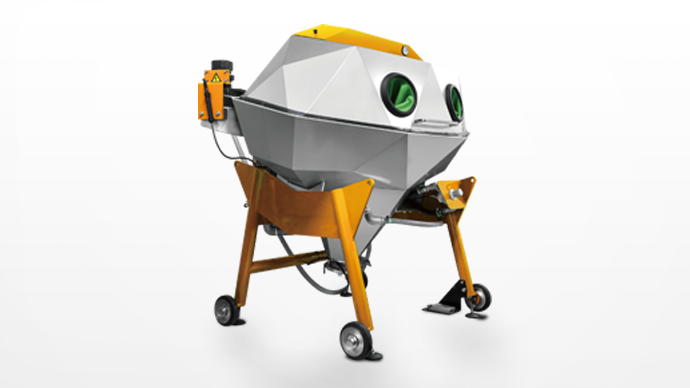
Manual Wet Blasting System for Large Workpieces
This compact manual wet blasting system for large workpieces relies on wet blasting technology and allows use with various abrasives for applications ranging from gentle cleaning to heavy processing.
-
Wide Body Allows Easy Handling of Even Long Items.
- The processing area is 1.6 times larger than previous systems, allowing items even more than 1 m long to be processed.
-
High Durability
- The parts of the body that come into contact with abrasives feature stainless steel for high resistance against corrosion and blasting wear.
- The pump interior and piping components incorporate highly wear-resistant urethane rubber.
-
Compatible With a Wide Range of Uses
- Can also be used with highly abrasive polygonal abrasives as well as with spherical abrasives such as glass beads.
- The material has a wide range of applications beyond cleaning and degreasing, including grinding, exfoliation, and satin finishing using edged particles.
Main Applications and Workpieces
- Cleaning engine parts prior to overhaul
- Cleaning vacuum pumps and contamination plates prior to maintenance
Surface Improvement (Plating, Painting, Coating Pretreatment)
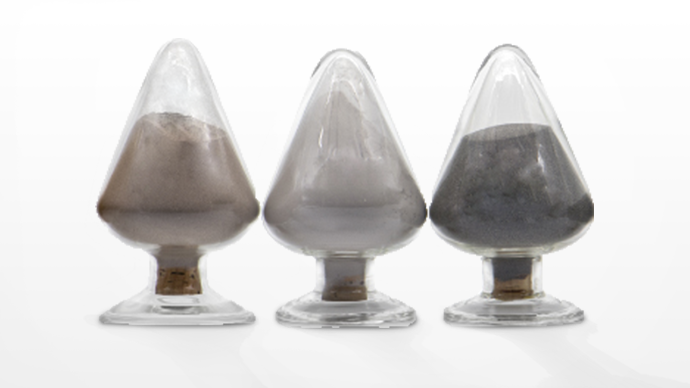
Improving Adhesion to Super Engineering Plastics, Cfrp, and Glass
Boosts coating adhesion for all kinds of materials, including super engineering plastics, CFRP, metals, and ceramics by harnessing the anchoring effects of nano-scale roughness unaffected over time, coupled with a cleaning capability that strips away thin layers together with surface contamination.
Features
-
Effective With All Kinds of Materials
- Allows treatment of all kinds of materials, including resins, metals, and ceramics.
-
Nano Anchoring Effect
- Generates nano-scale roughness to produce anchoring effects.
-
Free of Chemicals
- Physically etches the target material without use of chemicals.
-
Not Time-Dependent
- Improving adhesion by physically altering the surface profile results in lasting effects.
-
No Degeneration
- No processing heat is generated due to particle collisions or friction, eliminating degeneration.
Main Applications and Workpieces
Plating Onto PPS
- Shield plating onto PPS (super engineering plastic)
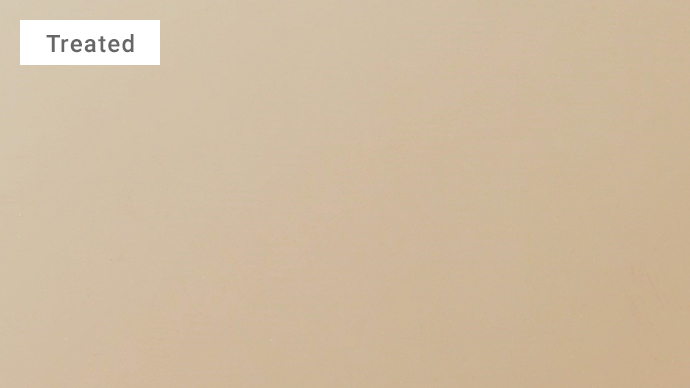
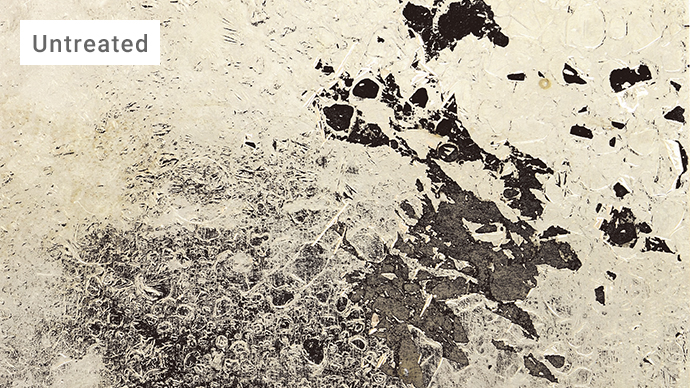
Painting CFRP
- Results of checkerboard painting test on CFRP
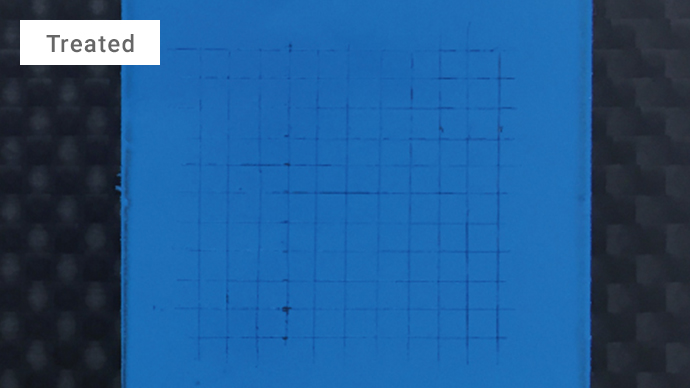
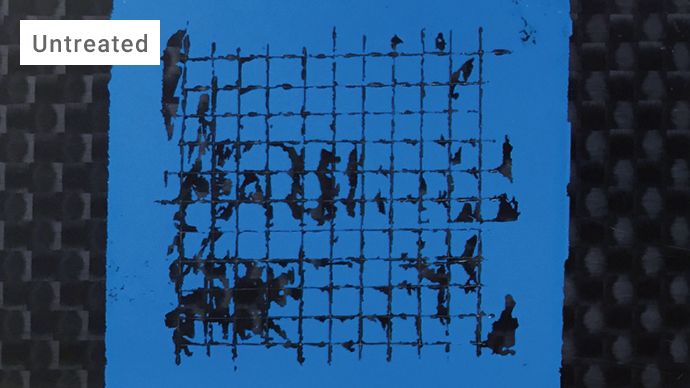
Ti Film Deposition
- Ti plate film deposition on glass surface
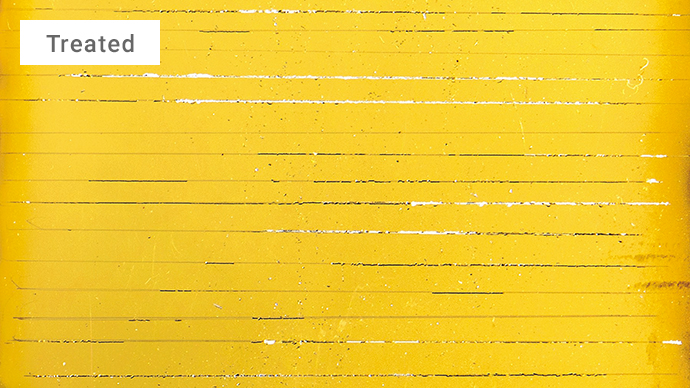
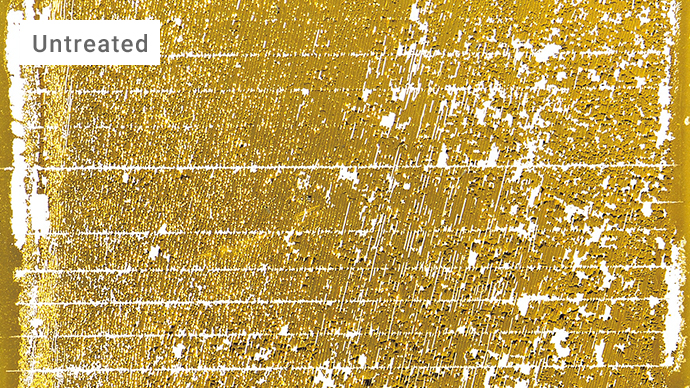
Laser Processing System (Marking, Deburring, Resin Removal)

Lower Semiconductor Defect Rates Achieved Using Laser Irradiation
This system is designed to print semiconductor component products. It allows printing on components for each frame and frames, individual components, and two-dimensional code printing. Laser irradiation can also be used to deburr resin components and remove resin. Resin removal is traditionally a process performed using dies. However, in addition to reducing semiconductor defect rates, a laser system helps eliminate die maintenance requirements (for example, replacement work associated with die and punch wear).
Main Applications
Used in processes to print product names, manufacturer names, and lot numbers on package surfaces, primarily after cutting out individual packages and forming leads
Typical System Configuration
- Frame supply unit
- Orientation/product confirmation unit (option)
- Laser marking unit
- Visual inspection unit (option)
- Brush unit (option)
- Frame storage unit
Please inquire for more information on deburring systems/wet blasting systems and laser deburring systems.
Electronics Equipment Department
Tokyo
81-3-5405-5781
Osaka
81-6-7637-3072