Machinery / Joining and Cutting Technologies
Technologies Solutions
Iwatani operates a welding demonstration room at its R&D Center, where it conducts demonstration tests of arc and laser welding technologies, and proposes solutions to welding issues. Kohtaki Corporation, a cutting equipment manufacturer of the Iwatani Group, provides a range of high-precision cutting technology solutions.
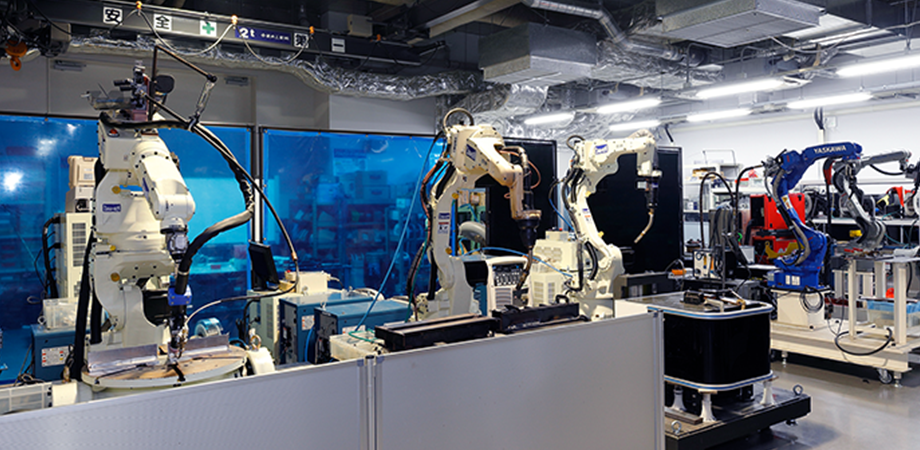
Welding Technology Solutions
We have been developing our welding businesses, such as for oxygen welding and welding rods, since our founding in 1930. Developments have included new welding technologies alongside the three major elements of welding, which are shield gas, welding machines, and welding rods. At Iwatani R&D Center, we also propose welding solutions for various base materials that integrate construction technologies developed in the manufacturing of gas tanks and containers. Iwatani continues to develop technologies that achieve high levels of spatter reduction, reduced slag, improved speed, and defect prevention to select the optimal welding materials for diverse welding scenarios. We deliver technical solutions based on an unmatched track record of deliveries to various welding companies, including for spatter reduction, improved weld penetration, blow hole prevention, and slag countermeasures.
Examples of Solutions
Here we introduce some examples of how our welding technologies can solve issues in welding.
Spatter Reduction Technology
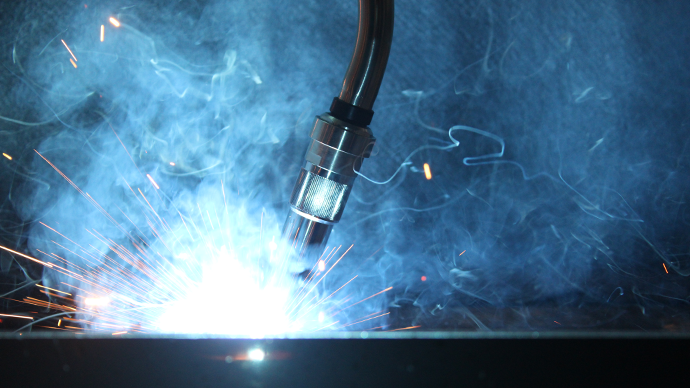
Before spatter countermeasures
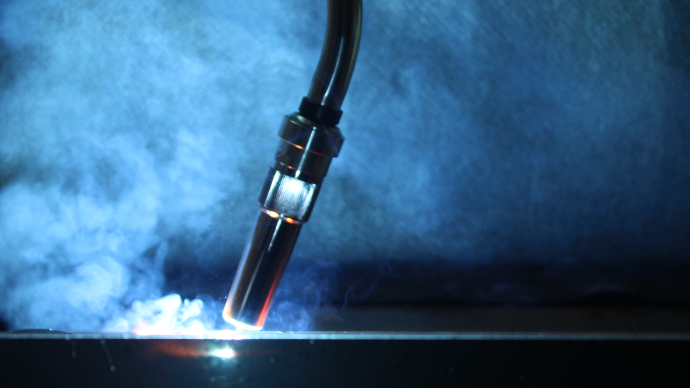
After spatter countermeasures
Of the various spatter reduction technologies, we first recommend the shield gas optimization. For general soft steels, changing from carbon dioxide gas to Acomgas (MAG mixed gas) will dramatically reduce the amount of scattered and adhering spatter. Even with carbon dioxide gas, spatter has been significantly reduced by combining it with the latest digital welding power supply. In addition to reducing spatter through the selection of wires, a combination of gas, power supply, and wire, the three major elements of welding, play an important role, improving weld penetration and suppresses defects. We propose solutions that incorporate welding methods, and invite you to try them.
High Quality Welding Technology of Plated Steel Sheets
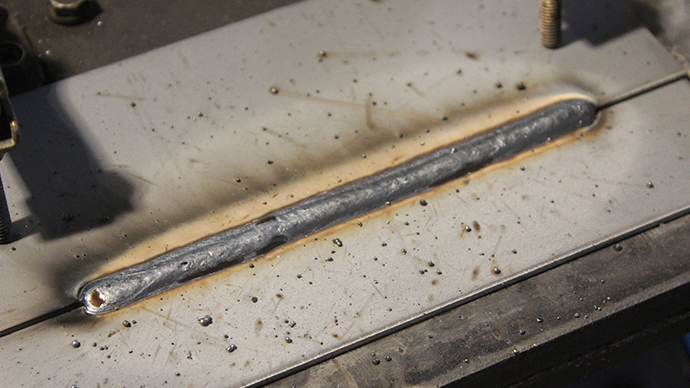
CO2welding of GA steel sheet
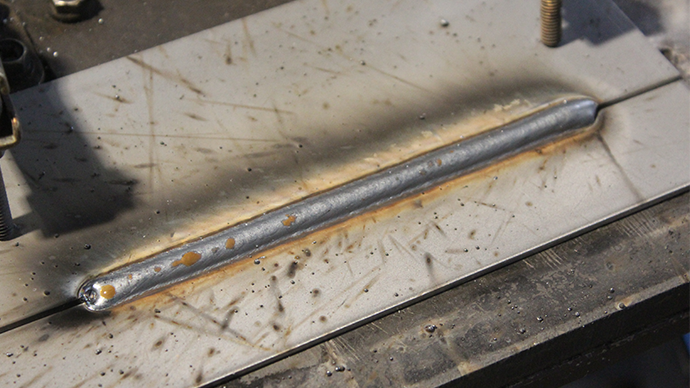
MAG welding of GA steel sheet
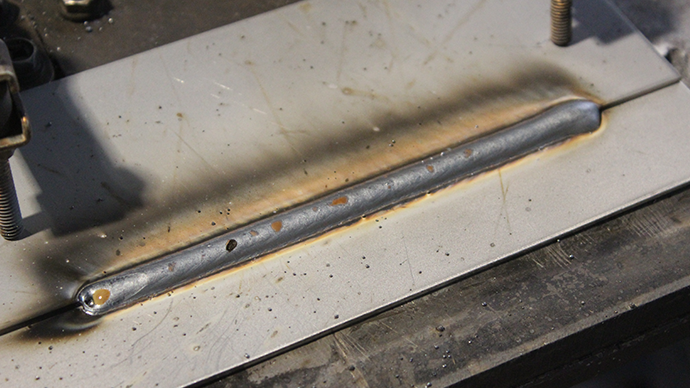
Wire supply control method
Technologies associated with surface-treated steel sheets such as zinc plating and GA have continued to evolve. In addition to increasingly rigorous regulatory requirements, rust prevention performance has increasingly become incompatible with weldability. Iwatani has evolved the development of special gas for zinc-plated steel sheets, significantly reducing spatter and slag by combining various wiring and welding methods. We invite you to try our welding solutions that suppress the types of blow hole that are directly linked with strength issues.
Slag Reduction Technology
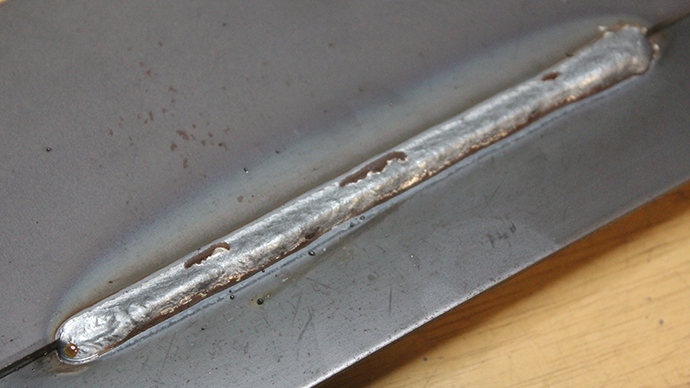
Before slag countermeasures
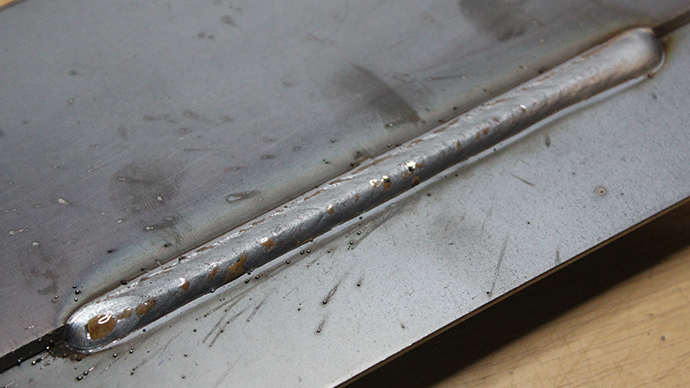
Mixing gas and no plated wire

Using Acom HT
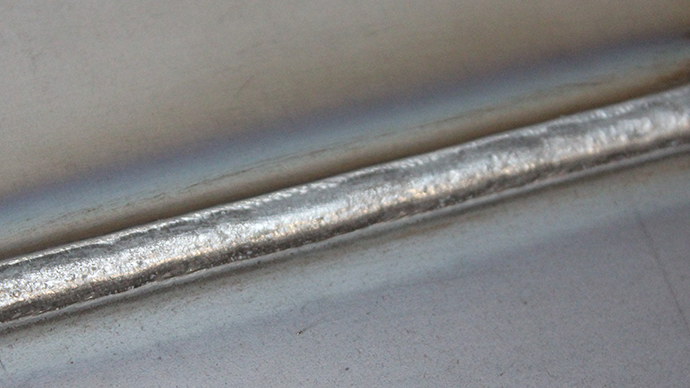
Pulse welding using low slug wire and Acom HT
Slag is the scab-like substance formed on a weld bead. Because it repels paint and exposes the bare metal, a hard glassy slag is a major cause of corrosion. Slag incorporates Si and Mn as deoxidizing substances but does not contribute to weld quality. We propose welding methods that greatly suppress slag generation through the combination of technology and welding material. Iwatani has also introduced a special wire that can be electrodeposited in combination with MAG gas. We invite you to try our welding solutions that reduce costs associated with post-processes.
High Quality Aluminum Welding Technology
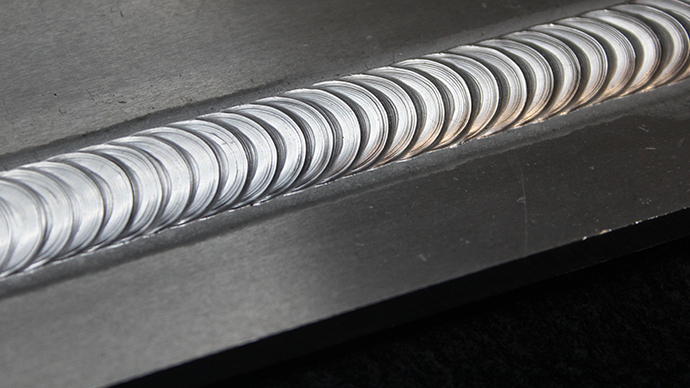
Achieves excellent bead appearance by pulse welding

Achieves deep weld penetration and attractive bead appearance with Hi-almate S
Use of aluminum has expanded in virtually every industry, including automobiles and Shinkansen trains, which are undergoing rapid weight reduction. However, aluminum welding used to join structures poses several issues, including blow holes and welding speed (good heat conduction affects weldability). We developed Hi-almate, a mixture of argon and helium, to improve penetration and melting speed, improving welding efficiency. The manufacturing know-how we have gained as a gas manufacturer has clear applications in suppressing blow holes. The material and handling of supply pipes have significant effects on the internal quality of aluminum welds. We invite you to consider trying welding control that draws on gas purity management know-how, which is the trump card for suppressing blow holes.
Welding Fume Reduction Technology
Welding fumes represent the most important issue involving improving welding environments. Completely sealing off fumes (a metal steam) generated during welding work poses major challenges. In response, Iwatani R&D Center has conducted extensive research into identifying welding materials and welding methods that can improve the welding environment. Our R&D Center has developed a welding fume reduction technology that integrates gas, wire, and welding methods. Drawing on materials free of substances harmful to humans wherever possible and repeated measurements in each welding method, we have managed to more than halve the volume of fumes generated. As a result, we propose our fume reduction technology, named FCT (Fume Cut Technology) in order to improve the welding environment, and invite you to try it.
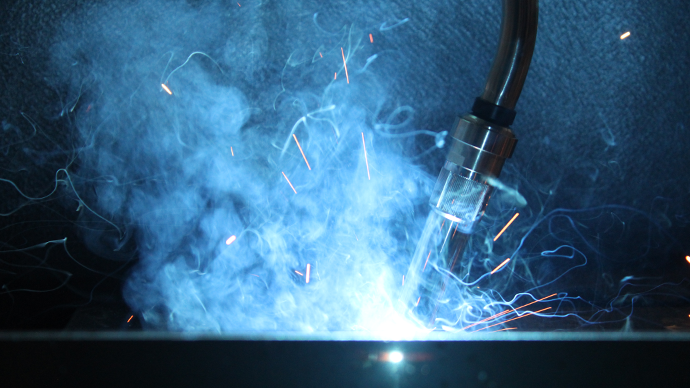
Before fume countermeasures
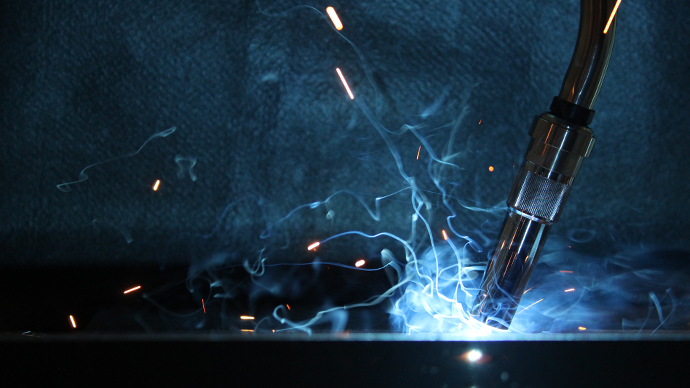
After fume countermeasures
Joining Technology Solutions
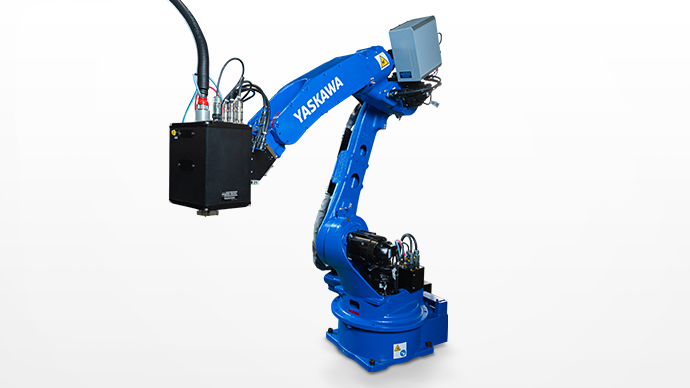
Laser Welding
Drawing on technologies cultivated through years of achievements, we propose optimal welding solutions by combining domestic and overseas oscillators, robots, jigs and devices to achieve high quality and high speed.
Handling
CO2, MAG, MIG, TIG, plasma, laser, brazing, friction stir
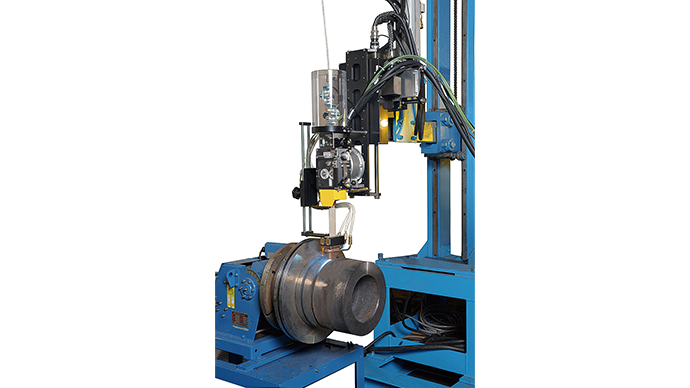
Other Joints
We propose joining and fastening methods for dissimilar metals and materials for which demand has grown in recent years, including joining, welding, and caulking.
Handling
Adhesive, sealant coating device (high precision metering pump), ultrasonic welding, caulking
Cutting Technology Solutions
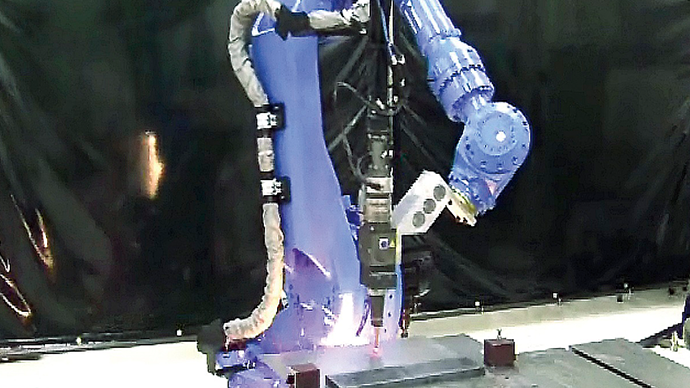
Laser Cutting
We propose thermal cutting solutions based on gas, plasma, and lasers, as well as cutting with special molds/cutters. These solutions account for workpiece shape and materials and can be tailored to meet special customer requirements.
Manufacturers Represented
Kohtaki Corporation, Mitsubishi Electric Corporation, Fuji Machine Works Co., Ltd.
Iwatani R&D Center
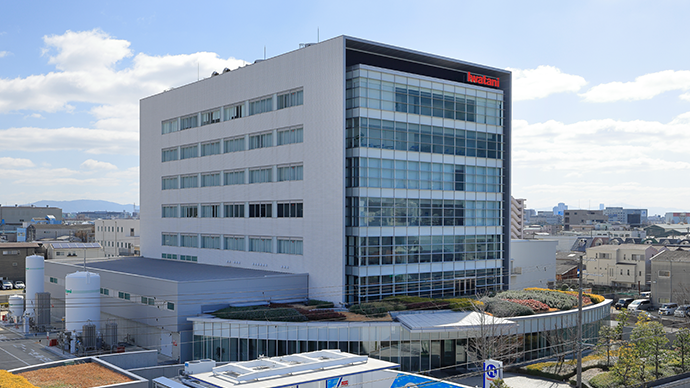
In April 2013, we established Iwatani R&D Center as a research and development base in Amagasaki City, Hyogo Prefecture. Here we offer a suite of world-class analytical equipment and a broad range of test environments for research and development efforts undertaken in partnership with our customers. We operate a welding demonstration room, where we showcase solutions for various welding issues.
Iwatani R&D Center Welding Demonstration Room
To meet specific customer requirements, we propose optimal welding solutions based on shield gas, mild steel, stainless steel, aluminum and other welding materials sourced from domestic and overseas welding manufacturers, state-of-the-art welding machines, and robots.
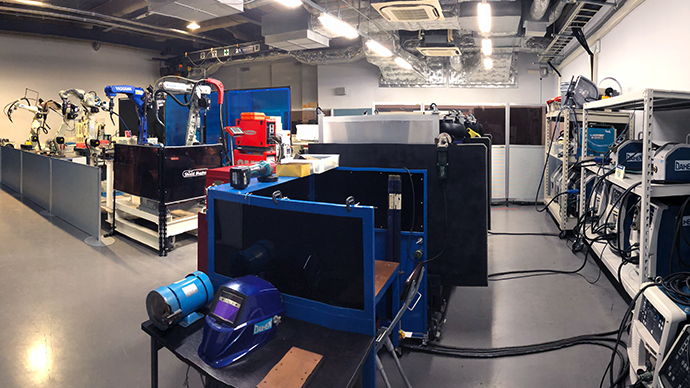
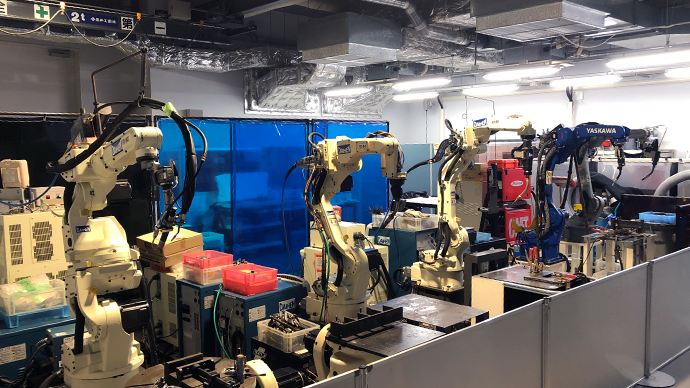
Kohtaki Robot Welding Demonstration Room
The demonstration room operated by Kohtaki Corporation (an Iwatani Group member) features a lineup of state-of-the-art robots, the foundations of a broad range of welding, cutting, sealing, and welding inspection solutions tailored to meet specific customer requirements.
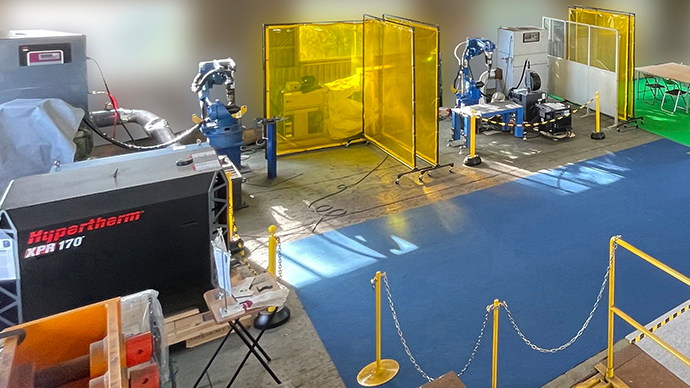
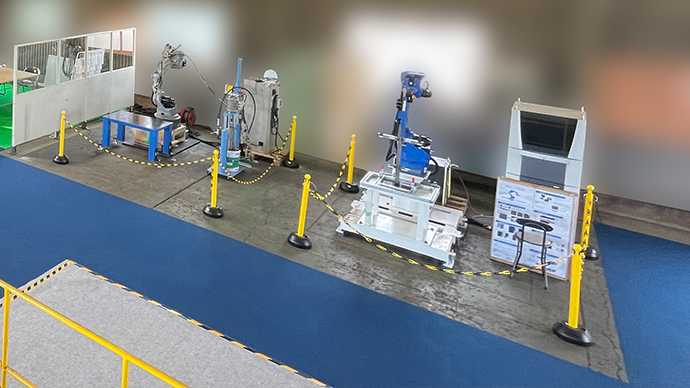
Joining and Cutting Technologies Product List