Iwatani R&D Center
Research and Development
Working with state-of-the-art analytical and testing equipment and experimental environments, we promote research and development efforts with universities and public institutions, as well as customers and partner companies from a diverse range of fields, including automotive, semiconductor, medical, and food industries.
Welding
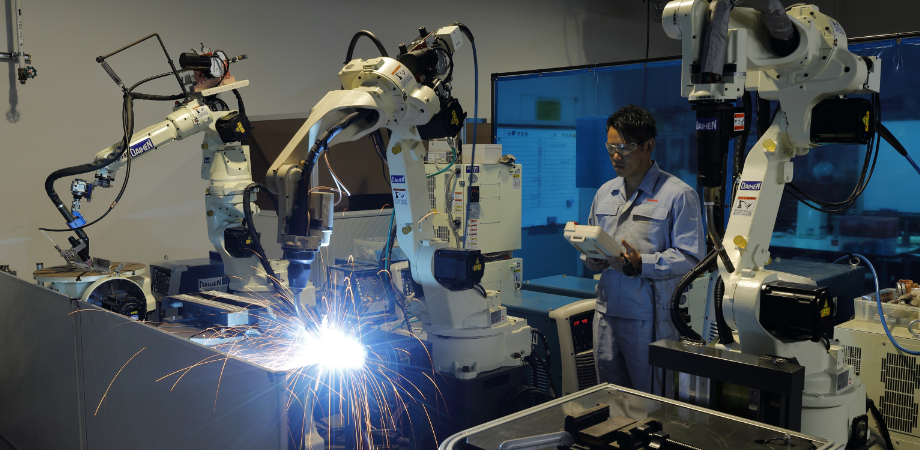
Welding Technologies Approached from Multi-Faceted Perspectives
Welding is a common process in metal processing. More than 60 different welding methods are currently in use.
In arc welding and laser welding, both representative welding methods, the quality of the welded joint depends on the combination of the welder machine, welding wire, and shielding gas. At the Iwatani R&D Center, we propose optimal welding methods combining these three factors to meet the specific needs of our customers.
Shielding Gases
Shielding gases for welding are used to protect the weld area from bonding between the molten metal and atmospheric components (oxidation, nitridation).
Since components of the shielding gas influence the heat source for the welding process, we can improve productivity by adjusting the composition of the gas mixture. High purity shielding gas enables the quality welding results required for semiconductors and fuel cells.
As the targets of welding become lighter and joint shapes become more complex, it has grown increasingly difficult to provide solutions based solely on the performance of welding machines. This has led to the growing importance of shielding gas performance. Our Shield Master® Series are proprietary shielding gas products.
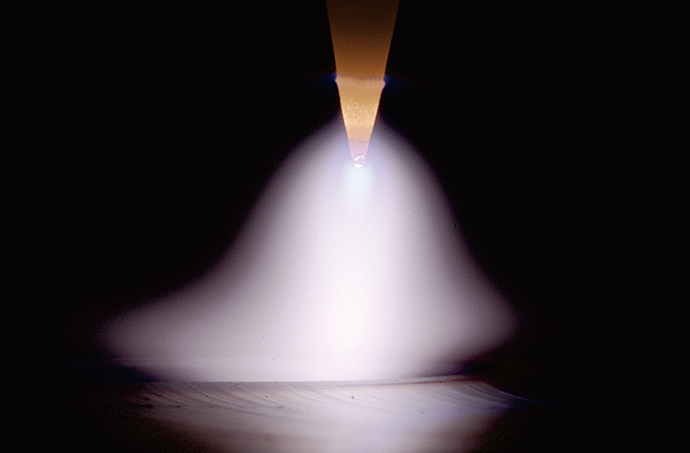
Welding Machines and Wires
To meet the wide-ranging needs of our customers, we provide optimal welding solutions by identifying the perfect combination of wire products made of mild steel, stainless steel, aluminum, and other materials from manufacturers in Japan and overseas; state-of-the-art welding machines and robots; and various shielding gases.
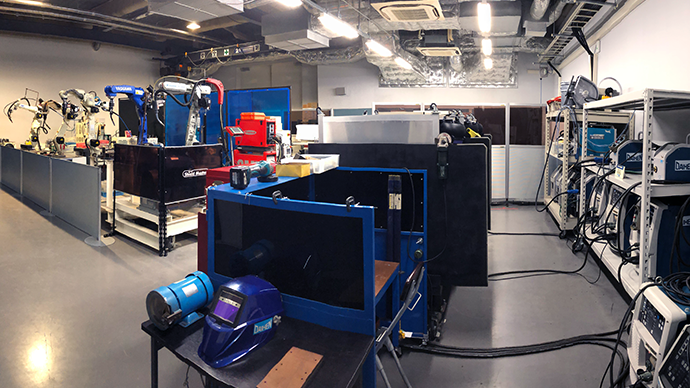
Semiconductors and Electronic Components
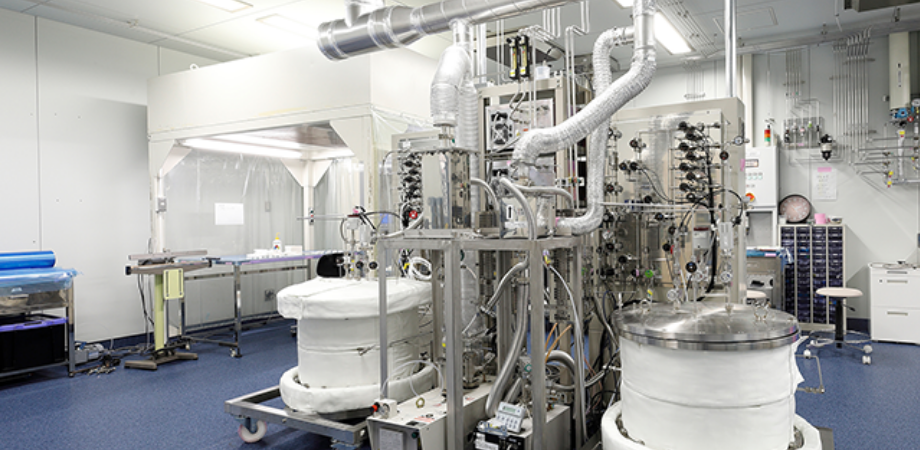
Gas Technologies Supporting Semiconductor and Electronic Component Production
Developed for semiconductor manufacturing, Iwatani’s proprietary cleaning gas—ClF3 (chlorine trifluoride)—has been adopted by semiconductor manufacturers around the world as a non-plasma cleaning technology that minimizes equipment damage.
We are also contributing to the manufacture of semiconductors and electronic components with our unique gas technologies. These include manufacturing and storage technologies for high-concentration ozone at concentrations of 50% or above, previously deemed impossible, as well as technologies involving deuterium gas manufacturing, for which demand is expected to grow in line with anticipated improvements in semiconductor performance.
ClF3 Gas Etching
Etching with ClF3 can be performed by simply spraying onto the substrate. This allows microfabrication without associated damage from plasma or other sources. Capable of overcoming various issues associated with the plasma process, including electrical damage, insulating film breakdown, and impurity contamination, this technology is expected to replace the plasma process widely used in semiconductor device processing.
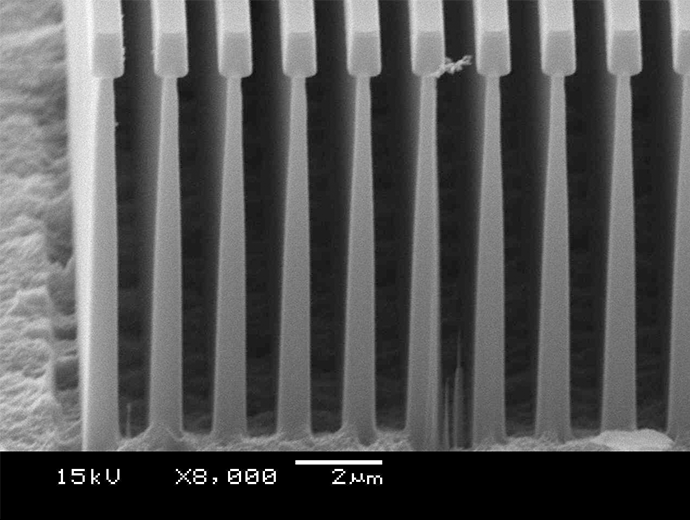
Cross-section of wafer after cluster etching
Ozone Passivation®
Ozone Passivation®, our revolutionary proprietary surface treatment technology, forms a dense oxide passivation film with mere exposure of the surface to high-concentration ozone gas at room temperature. Since the gas treatment is performed at room temperature, it is also effective in forming films inside pipes after welding and in forming films for microfabricated parts. The improved corrosion resistance helps suppress metal contamination and reduces parts maintenance requirements.

Manufacturing and Development of Deuterium Gas
Composed of a stable isotope of hydrogen, a common industrial gas, deuterium gas is widely used in industrial processes and in research and development in various fields, including electronics and optical fiber production. We pursue research to establish manufacturing and analysis technologies to achieve a stable supply of deuterium gas, which offers characteristics dramatically different from hydrogen, as well as to improve production efficiency.
Summary of Deuterium Gas
Packaging type | 47 L seamless gas cylinder |
---|---|
Content | 7,000 L |
Purity | ≥ 99.995 % |
Isotope concentration* | ≥ 99.8 atomic % |
*Isotope concentration: D/(D + H)
(D: deuterium gas concentration; H: hydrogen gas concentration)
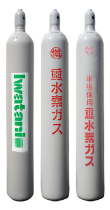
Regenerative Medicine
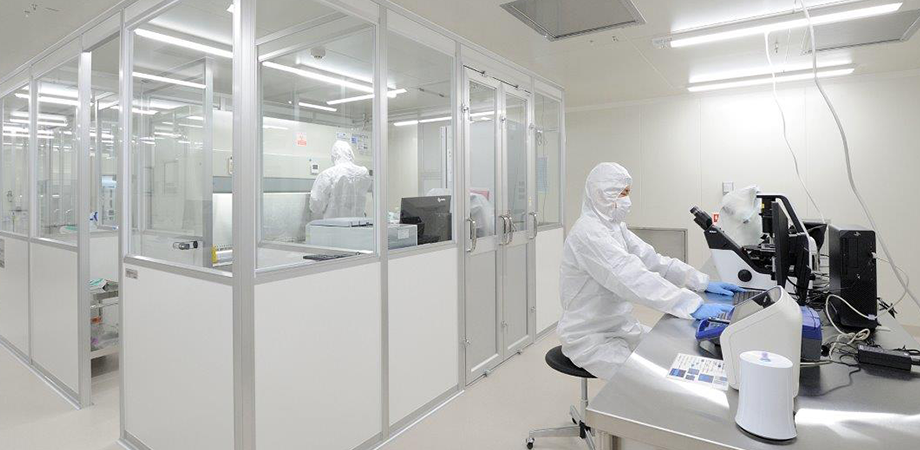
Development of Technologies and Instruments to Help Establish the Regenerative Medicine Industry
We are working to expand the use of cell storage and transportation systems based on the fundamental analytical and cryogenic management technologies cultivated over the years.
In April 2020, in partnership with Osaka University, we founded the Joint Research Laboratory for Cell Storage and Transport Technology. We are currently developing technologies and equipment for cell storage and transportation, with the ultimate goal of commercializing regenerative medicine technologies.
In February 2022, a cleanroom was installed at the Iwatani R&D Center to reproduce and evaluate the series of processes performed at cell manufacturing plants—from cell culture, freezing, storage, to transportation.
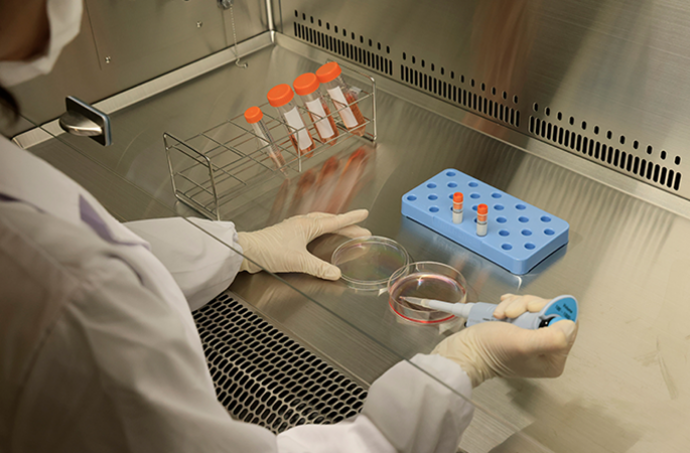
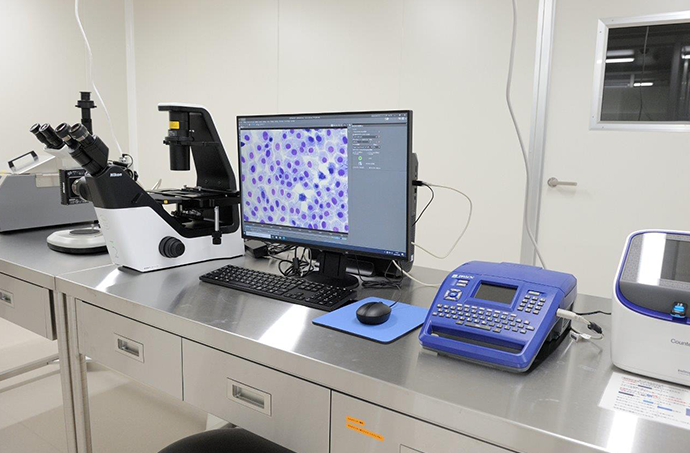
Analysis and Quality Evaluation
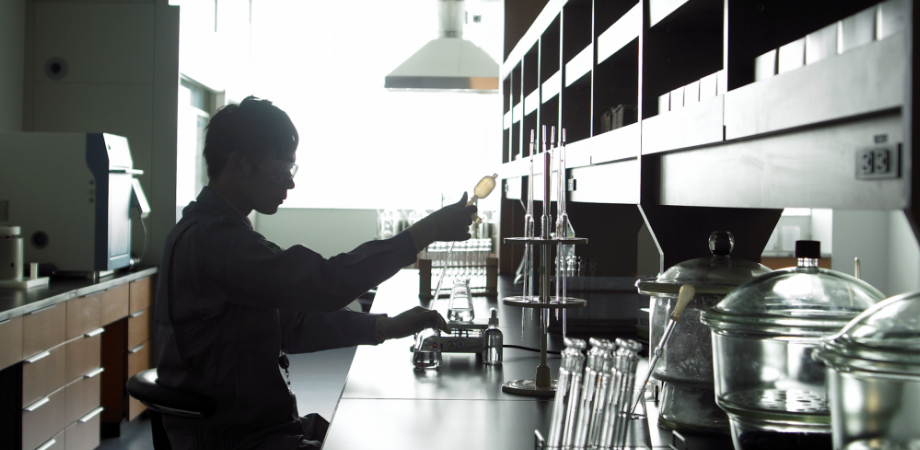
Analysis and Experimental Environment for Development Needs Across Diverse Fields
State-of-the-art experimental and measurement facilities are key to the research and development capabilities of the Iwatani R&D Center. The center offers a multifunctional, multipurpose experimental environment equipped with large laboratories, environmental testing rooms, and cleanrooms, as well as precision analytical instruments for various fields from nanoscale material analysis to ultraprecise gas analysis. Our cutting-edge analytical and experimental environments help create new technologies for the next generation.
Fundamental Technologies for Advanced Analysis
Supported by our advanced analytical technologies, we are registered as an environmental measurement certification business and have acquired ISO 17025 international laboratory accreditation. As a gas supplier, we respond swiftly to inquiries for analysis of ultra-trace impurities in high purity gases.
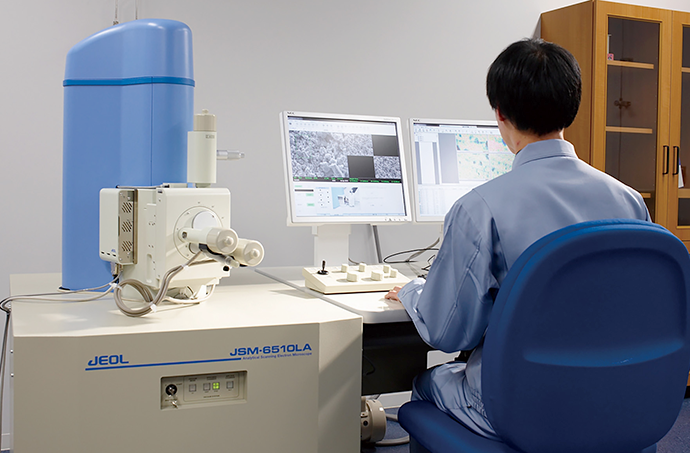
Quality Evaluation
We analyze and evaluate the caloric value and impurity concentrations of PKS (palm kernel shell), sold as fuel for biomass power generation. We also contribute to food safety through pesticide residue analysis and microbial analysis of frozen vegetables, processed marine products, and processed meat products. These analyses are carried out in addition to analyses of nutritional value, such as vitamin content.
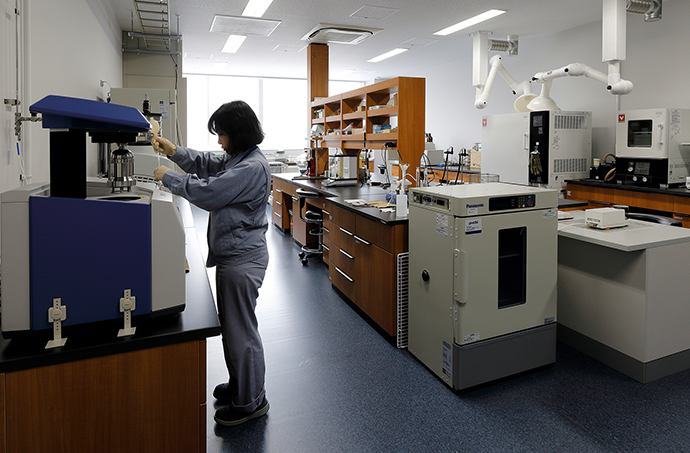